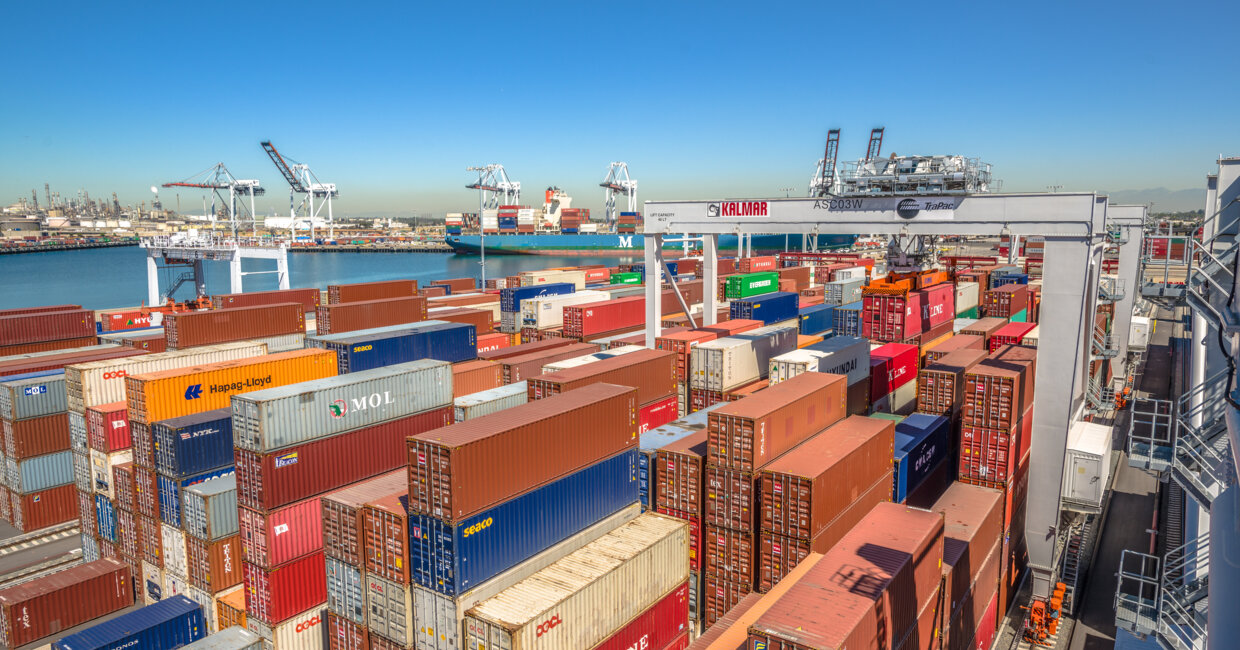
Designing safety
When designing automation systems for container terminals, Kalmar’s engineers have to bear in mind a high number of safety standards.
One of the most important factors holding back the container shipping industry today is the lack of global commercial standards for terminal automation. Kalmar supports global standardisation, and safety standards are a key component.
Just like every Kalmar machine, every Kalmar automation system undergoes a risk analysis where the necessary safety measures are clearly defined. Since the early 2000s when Kalmar tested its first automated terminal equipment in Australia, machine standards have developed considerably, and increasingly the focus is on product safety.
“For example, system standards for cranes, crane access or the design of safety related control system parts constitute an integral part of our terminal automation R&D. Today, there are tens of standards which we refer to daily and which ensure that our solutions are in line with the European Union’s Machinery Directive. Regional safety regulations around the world differ from the EU to only a small degree. We naturally take possible differences into consideration in our global deliveries,” says Reetta Jokinen, Safety Manager, Kalmar.
Strict guidelines do not stifle creativity
Standards provide guidelines. With all standards, there is always some room for interpretation. However, it may happen that if you interpret safety standards too rigidly, equipment will indeed feature ultimate safety, but may not perform well. On the other hand, if you interpret standards too freely, you will always worry about what could go wrong. With long experience in product safety engineering, Kalmar has created a level of risk assessment to achieve the right balance in following safety standards.
”A good standard does not limit product or system development or engineers’ creativity. In each customer case, the target is always to find a safe solution. By following set standards, we can be sure that it happens,” adds Jokinen, who represents Kalmar on the Finnish National Standards Committee on Cranes.
The committee has recently been revising one of the most important standards in terminal operations, the crane standard EN 15011, which comes into force in early 2018. It will be a harmonised standard to provide one means for bridge and gantry cranes to conform to the essential health and safety requirements of the Machinery Directive as mentioned in Annex ZA.
Machine standards have developed considerably, and increasingly the focus is on product safety.
Eagerly anticipating the new standards
One of the recent R&D projects that involved a lot of work with safety standards was on automating the Kalmar RTG crane. The outcome of this successful project was the Kalmar AutoRTG System.
“Unlike the manual crane, the new automated crane has more safety functions with which the machine itself takes over responsibility for safety. We improved our process to ensure that safety functions fulfil the requirements set by the latest standards to improve and enhance our engineering work. It involved a complete risk analysis process all the way from hazard identification to a final safe design solution,” says Sakari Koivumaa, Senior System Safety Engineer, Kalmar.
Jokinen and Koivumaa are well aware of all machinery safety aspects as they are both Certified Machinery Safety Experts (CMSE®). This globally recognised qualification makes possible a 360° approach to machinery safety.
“We eagerly look forward to getting certain standards, such as an updated version of safety requirements for driverless industrial vehicles. In the case where there are no set standards for a solution which you are designing, you can get good guidance for assessing risk from standards that have set requirements for a similar kind of solution,” Koivumaa adds.
Both safety experts would like to see more safety-rated components for outdoor conditions. For example, whereas automated guided vehicles can operate as mixed traffic (manual and automated combined) in indoor surroundings, such as factories or warehouses, outdoor terminal equipment cannot, at least not as freely. Fences are still needed around outdoor terminal areas.
Related articles
Subscribe and receive updates in your email
Subscribe