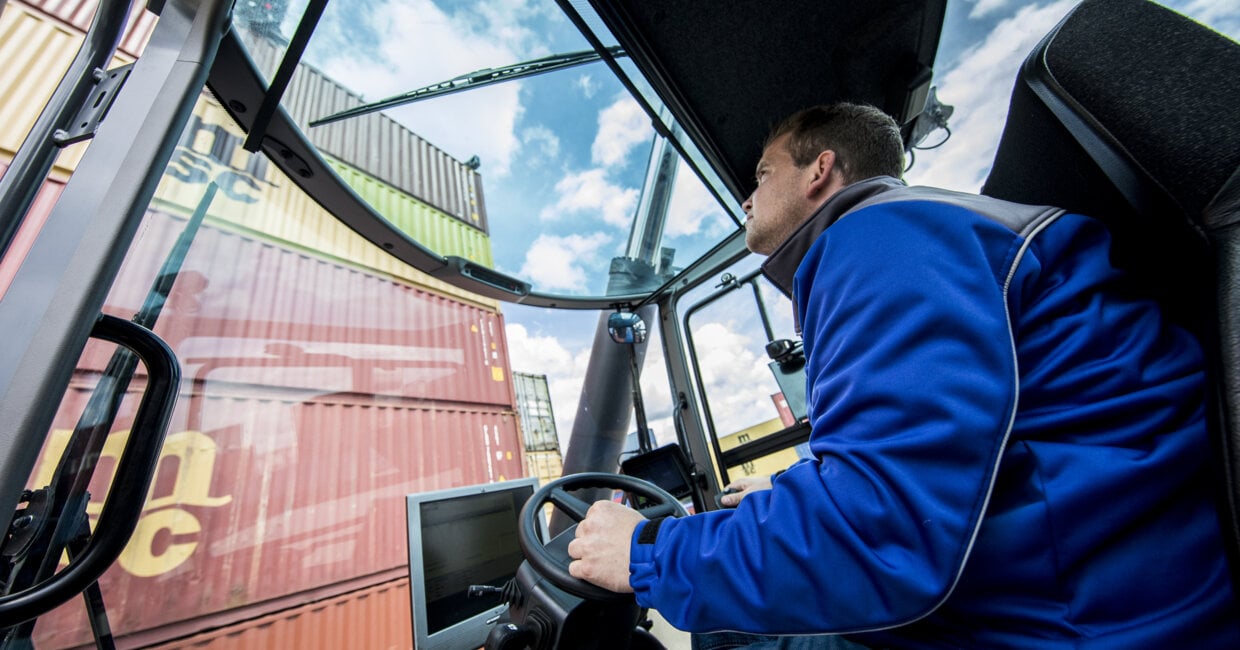
Quick-wins in mobile equipment eco-efficiency
Zero-emission equipment is the ultimate goal in cargo handling. In the meantime, there are many steps you can take to reduce the CO2 emissions of mobile equipment right now. Two such steps with immediate payoff are visualising fuel consumption and training operators to drive eco-efficiently.
Per-Erik Johansson, Technology Manager, Electrification at Kalmar Mobile Solutions, says, “Fully electric and hybrid solutions in container stacking areas and horizontal transportation are already a reality. However, I would estimate that more than 90% of the industry’s mobile equipment will still be diesel driven for years to come.”
“Reducing fuel consumption in smaller equipment could have a huge impact while we develop pure zero-emission alternatives for reachstackers and other mobile equipment,” Johansson emphasises.
Mette Kjems Baerentzen, Product Portfolio Manager for Kalmar’s Counterbalanced Container Handlers, lists several steps that every cargo handling company can take today to reach extensive CO2 reductions and improved equipment lifetimes in mobile equipment. These include retrofitting fuel reducing solutions to existing equipment, training operators to drive eco-efficiently, setting fuel consumption company targets, and visualising driver performance related to targets.
Added together, these measures can reduce fuel consumption of current equipment by up to 20%.
“Take, for example, an average reachstacker that has 2000 running hours per year and consumes 18 litres of diesel an hour. If it adapts these eco-efficiency measures, one machine will contribute almost 20 tons less CO2 a year,” Baerentzen explains.
"These measures can reduce fuel consumption of current equipment by up to 20%."
Put the pedal to the metal
Kalmar focuses on three areas to help customers achieve a better CO2 footprint: emission efficiency, systems efficiency, and resource efficiency. Data is harnessed to boost progress in all three areas.
“At Kalmar, we see it as our responsibility to use our extensive data to turn it into valuable knowledge for our customers. Visualising driving data is a great example. Fuel consumption is very strongly linked to putting the foot to the pedal,” Baerentzen notes.
“I just put together an analysis for a customer whose data revealed extremely fast driving combined with idling over 40% of the time in their reachstacker operations. It was easy to recommend eco-efficiency upgrades that include speed limitations added to the machinery as a setting, and a feature that shuts down the engine after a minute of idling.”
Johansson and Baerentzen remind us that clearly visualising fuel consumption and training operators to drive eco-efficiently pay off right now – and will continue to do so once we reach electrification.
“Using data as a basis to train drivers will be just as important as we move towards electrification to minimise energy waste, which is the first step regardless of what else is done. You need to conserve energy to maximise battery lifetime and ensure all-important uptime,” says Johansson.
“Kalmar’s digital solutions for daily inspections ensure our customers can pick up on what is happening in good time."
Eco-efficiency is not just about conserving energy. Extending the lifetime of existing products is also hugely important.
“Kalmar’s digital solutions for daily inspections ensure our customers can pick up on what is happening in good time. Here, something as simple as a tyre pressure monitoring system can make a considerable difference. If the air pressure is wrong, you will consume more fuel and wear out your tyres faster,” Baerentzen adds.
We all need to do our part
One R&D project that Johansson and Baerentzen are especially proud of is the Eco Reachstacker that Kalmar developed in partnership with Volvo Penta and Dana Rexroth.
“The Eco Reachstacker has a very innovative driveline. It’s diesel, but it saves a lot of fuel and actually outperforms the larger reachstackers. We have many customers who already say that the Eco Reachstacker is the only one that gets their company’s seal of approval,” Baerentzen says.
Kalmar’s goal is an all-electric future, with the entire portfolio available as electrically powered versions.
“We already offer electrically powered options for all the larger cranes, straddle and shuttle carriers, AGVs, forklift trucks, empty container handlers and terminal tractors. The development work is well underway for Kalmar reachstackers as well,” says Baerentzen.
“The electrically powered reachstacker will be in place in 2021, with serial production possible fairly soon after,” Johansson affirms.
Kalmar’s goal is an all-electric future, with the entire portfolio available as electrically powered versions.
In the meantime, Johansson reminds us that biofuel is a viable option for all Kalmar products already today, although the availability of biofuel varies from country to country. Lithium-ion batteries with plug-in charging are also available for numerous equipment, including light and medium forklifts and terminal tractors.
Whichever options you choose, Johansson and Baerentzen encourage taking immediate measures to enhance eco-efficiency for smaller cargo handling equipment:
“It’s midnight. We have been living on borrowed resources for far too long. Why wait another minute when so many feasible opportunities for CO2 reductions are already available? Mankind needs to take responsibility. Everybody needs to do what they can to create a liveable world for our children and grandchildren,” Johansson concludes.
Related articles
Further reading
Subscribe and receive updates in your email
Subscribe